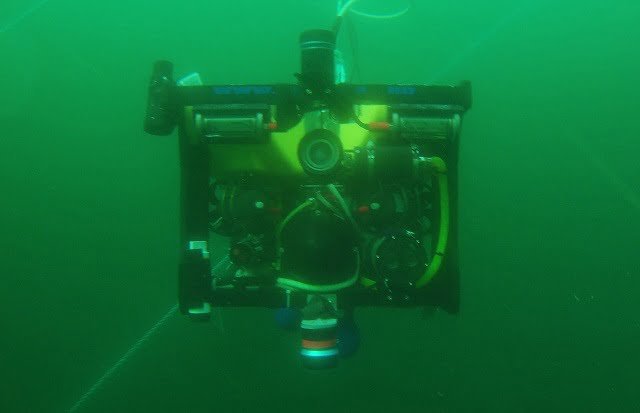
Researchers from SINTEF Ocean and NTNU have published a study exploring a decade of research conducted at SINTEF ACE, an industrial-scale aquaculture laboratory. By sharing lessons learned and future perspectives, the researchers hope to spark greater interest in the use of robotics, a technology with immense potential to revolutionize aquaculture.
The study uses Norway as an example. Since the 1970s, its aquaculture industry has experienced a boom, becoming its second most important export after oil and gas. Atlantic salmon is its main player and thrives in floating fish farms along the coast.
Fish are typically raised in large net cages along the coast or in open sea. These cages, exposed to waves and currents, require constant monitoring and maintenance. Traditionally, divers performed these tasks, but this method is risky and expensive. Moreover, stricter regulations and the lack of suitable coastal sites are pushing fish farms farther offshore, where weather conditions are harsher.
Unmanned Underwater Vehicles (UUVs) to the rescue
Safety concerns and stricter regulations in salmon farm operations are pushing the industry towards Unmanned Underwater Vehicles (UUVs), such as remotely operated vehicles (ROVs). These ROVs are like underwater robots, controlled by humans from the surface.
ROVs have become a cornerstone for Norwegian salmon farmers, addressing tasks such as:
- Net cleaning: Keeping nets free from biofouling (accumulated aquatic organisms) is crucial for fish health. ROVs can efficiently remove these unwanted hitchhikers.
- Mooring line inspections: Secure anchoring of net cages is vital. ROVs can meticulously inspect these lines for wear and tear.
- Fish monitoring: Monitoring fish health and well-being is paramount. ROVs provide valuable information for fish farmers.
The rise of autonomous fish farming
However, ROV operations are costly and risky. That’s why researchers are developing autonomous ROVs, capable of functioning without constant human control. This aligns perfectly with the concept of Precision Fish Farming (PFF). PFF aims to replace manual operations with data-driven decision-making and autonomous robots.
Imagine ROVs autonomously navigating through net cages, using advanced sensors to detect even the smallest hole. Research is ongoing, and projects are focusing on:
- Autonomous net inspection: Using sensors and cameras to autonomously find and assess net integrity.
- Smart navigation: Equipping net cages with navigation aids to help ROVs move freely.
- Robotic net cleaners: Researchers have developed robots that can crawl along nets and remove biofouling buildup.
Challenges of underwater robotics in aquaculture
Underwater robots have immense potential to revolutionize aquaculture. But like any new technology, there are challenges to overcome. Understanding these challenges paves the way for better robot designs and smoother operations.
Environmental issues: a tough workplace
The underwater world is unforgiving. Strong currents make robot control difficult. Communication is hindered by water, which weakens signals. Saltwater corrosion can destroy equipment. Even unpredictable weather hampers operations, increasing safety risks and limiting windows of opportunity.
Not all technology is equal: the case of underwater positioning
Acoustic positioning systems (USBL) are supposed to pinpoint a robot’s location. However, researchers have found inconsistencies. Sometimes, USBL works perfectly. Other times, signals are weak or unreliable. This seems to be due to how sound bounces and scatters underwater.
The key takeaway?
Adjust USBL settings for each environment, starting with low power and gradually increasing to achieve optimal signal strength. Additionally, be prepared for signal drops, so robots need robust backup systems.
Doppler Velocity Loggers (DVL) and net inspection
Doppler Velocity Loggers (DVLs) have proven useful for measuring a robot’s speed and distance relative to the fishing net. By increasing transmission power, DVLs can achieve “net lock,” providing accurate readings when sensor vision is not obstructed by fish. Even when fish shoals get in the way, outliers can be identified and discarded. However, DVLs only work close to the net (within 5 meters) and cannot be used on the seabed.
The challenge of underwater visibility
Aquaculture presents unique challenges for underwater cameras. Fish waste and uneaten food can cloud the water. Working near the surface introduces another variable: bright sunlight. These factors significantly affect image quality. For example, researchers testing a laser camera triangulation method for localization initially succeeded. However, subsequent tests failed because water clarity had decreased. Lesson learned: underwater cameras require careful consideration of water quality and lighting conditions.
Maintaining the robot’s “lifeline”
Handling the rope, the lifeline connecting the robot to the surface, is a demanding task, especially outside the net cage. Fish farm environments are filled with complex mooring systems, electrical lines, and feed lines. While it’s possible to perform inspections outside the net, they require constant vigilance to avoid entanglements in the straps. Often, it’s better to divide inspections into segments with fewer cables and ropes. One study even documented a strap entanglement caused by a sudden current surge when the ROV was unsupervised.
Sharing space: robots and fish
Inside the net cage, entanglement risks are lower, but operating the robot requires careful attention not to disturb the fish. Rapid movements can startle fish and cause them stress. Interestingly, studies suggest that fish may even learn to avoid areas where robots operate frequently.
Safety first: robot design matters
Robot design should prioritize minimizing damage to the net and fish. Sharp edges and tools are not allowed, as they can tear the net. Similarly, propeller cages are essential to prevent fish from getting caught in the propellers.
By recognizing these challenges and implementing lessons learned, researchers and engineers can continue developing better underwater robots for sustainable and efficient aquaculture.
Conclusion
The study presents findings from a decade of experiments conducted at SINTEF ACE. Researchers discussed lessons learned and future perspectives on aquaculture robotics, a field with immense potential to revolutionize the salmon industry.
The study was funded by the Research Council of Norway (RCN), SFI Exposed Center for Research-based Innovation, and funds from SINTEF RACE.
Reference (open access)
Amundsen, H. B., Xanthidis, M., Føre, M., Ohrem, S. J., & Kelasidi, E. (2024). Aquaculture field robotics: Applications, lessons learned and future prospects. arXiv preprint arXiv:2404.12995.

Editor at the digital magazine AquaHoy. He holds a degree in Aquaculture Biology from the National University of Santa (UNS) and a Master’s degree in Science and Innovation Management from the Polytechnic University of Valencia, with postgraduate diplomas in Business Innovation and Innovation Management. He possesses extensive experience in the aquaculture and fisheries sector, having led the Fisheries Innovation Unit of the National Program for Innovation in Fisheries and Aquaculture (PNIPA). He has served as a senior consultant in technology watch, an innovation project formulator and advisor, and a lecturer at UNS. He is a member of the Peruvian College of Biologists and was recognized by the World Aquaculture Society (WAS) in 2016 for his contribution to aquaculture.